General Information
Excellent technology right down the line
As a KRONES affiliated company, EVOGUARD has decades of experience in line construction under its belt for use in the development of its components. Yet EVOGUARD also incorporates completely new ideas in its engineering. Its motto: Only safe and reliable components are good enough for your line.
At a glance
- Innovative technology for valves, valve manifolds and pumps used in process and filling technology
- First-class KRONES quality at component level
- Manufacturing in accordance with the strictest quality and hygienic-design guidelines
- High efficiency
- Easy and reliable operation in everyday production
- Elementary modules for absolute process reliability
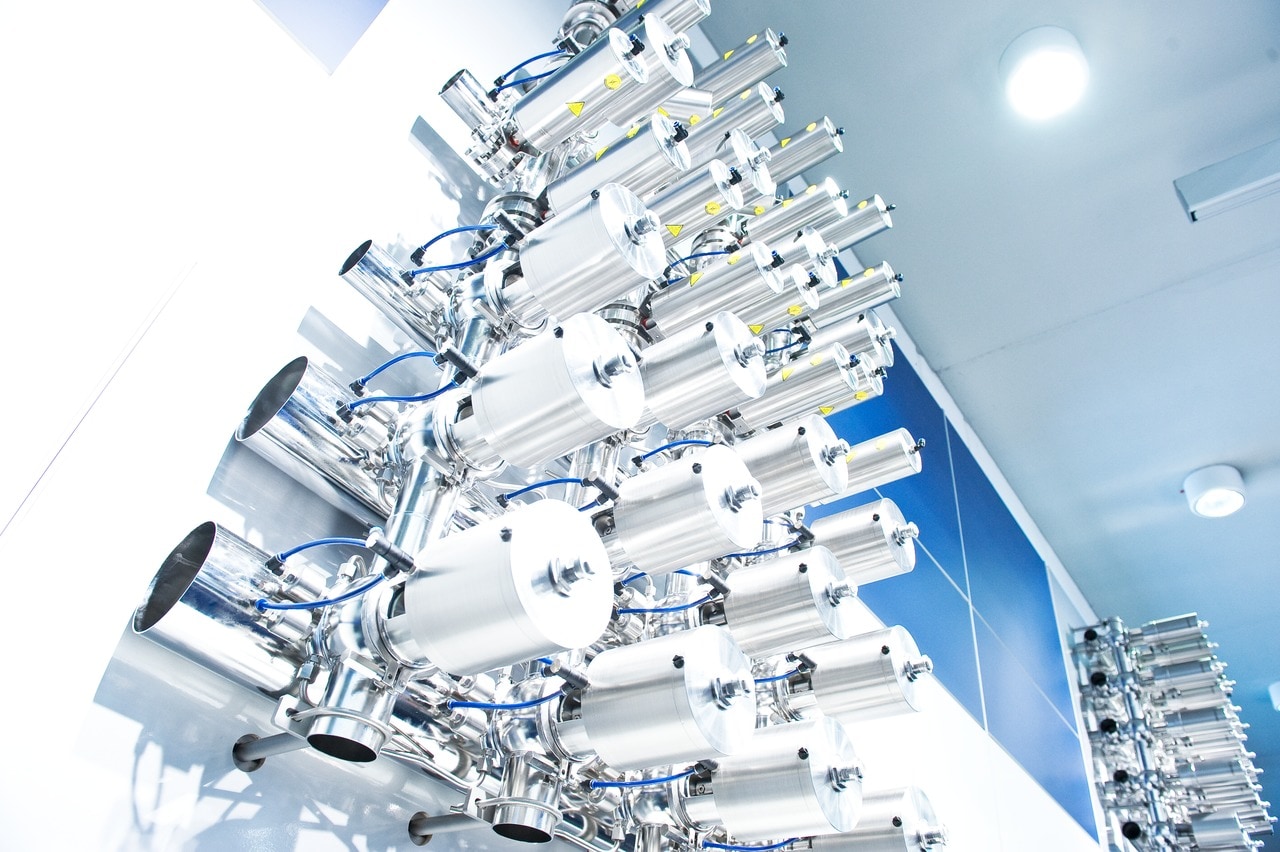
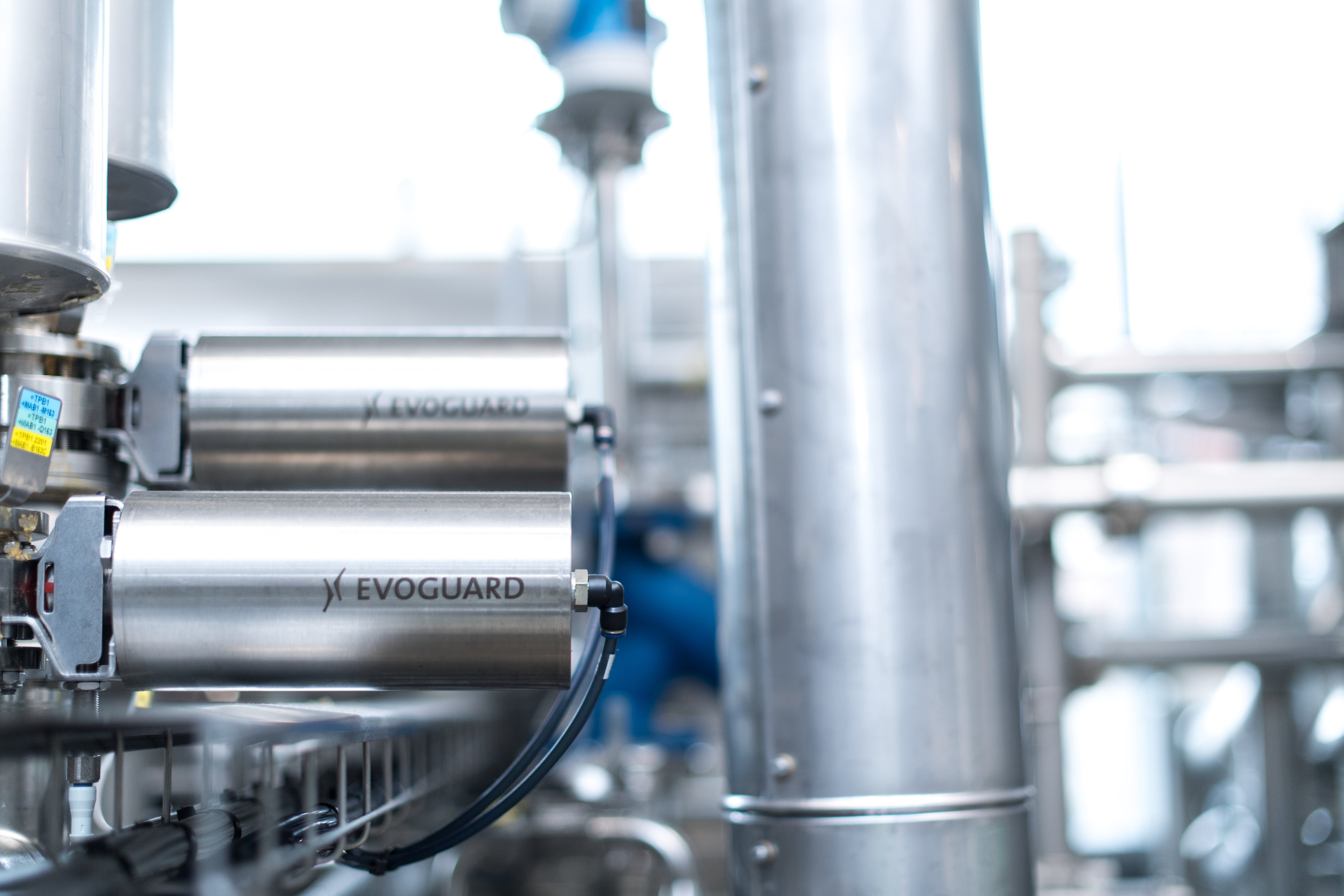
Where our products are used: the industries we serve
Where our strengths lie: process components
- Valves and valve manifolds
From the simple shut-off function up to the most advanced aseptic processes and complex valve manifolds: The EVOGUARD valve range combines hygienic and aseptic designs with all the requirements to meet demands on process stability, reliability, and maintainability.
- Hygienic centrifugal pumps
Gentle product handling combined with the highest efficiencies, robust design and easy maintenance underline the advantages of the EVOGUARD centrifugal pump series.
- Tank safety and cleaning systems
The modular design allows for the configuration of a solution for tank cleaning and safety that is tailored to the customer's requirements.
- Evotube tubular heat exchanger
Maintenance-free modules with cross-corrugated tubes ensure an efficient heat transfer combined with gentle product treatment. They are developed and manufactured by KRONES.
Selection
- Food and beverage industry
- ESL applications (Extended Shelf Life)
- Aseptic applications
Valves: Everything from one source – overview of our product range
Technical data
Benefits
Highest quality in the manufacturing process
- Manufacturing of the valve housings by chipping solid stainless steel material
- Accurate traceability and identification of parts by matrix code
- Use of tested materials with acceptance test certifications
Energy savings included
- Actuator variants in modular concept – adjusted to systems with a product pressure of 6, 10 or 22.7 bar
- Economical control air consumption for double seat mixproof valves with fast stroke movements for cleaning the leakage space
- Free cross-sectional areas in relation to the pipe diameter
Process safety
- Optimised sealing geometry, certified by the EHEDG
- Housings without dead space and optimally designed seal installation areas for hygienic production conditions
Consistent when it comes to safety demands
- Design according to the requirements of European Machinery Directive 2006/42/EC and Pressure Equipment Directive 2014/68/EU
- Design review by TÜV SÜD technical inspection authority (pressure, safety, strength testing, etc.)
- Pressure-resistant design of the housings of seat valves with PN 25 pressure rating
Safe handling during daily production activities
- Easy assembly and disassembly – without special tools
- Maintenance-free actuators in welded design
- Safe and quick spare parts replacement without risk of accident or confusion of seals